Can App-based inventory management technology improve business efficiency and productivity while increasing profit?
Who is this whitepaper for?
This paper provides information for businesses that carry inventory in stores and vans (for example, manufacturers and service providers such as Independent Housing Associations, their contractors, facilities management businesses and utility companies) that want to optimise their inventory to improve customer service, reduce costs and increase productivity by increasing the number of jobs that can be completed each day.
The challenges of Inventory Management
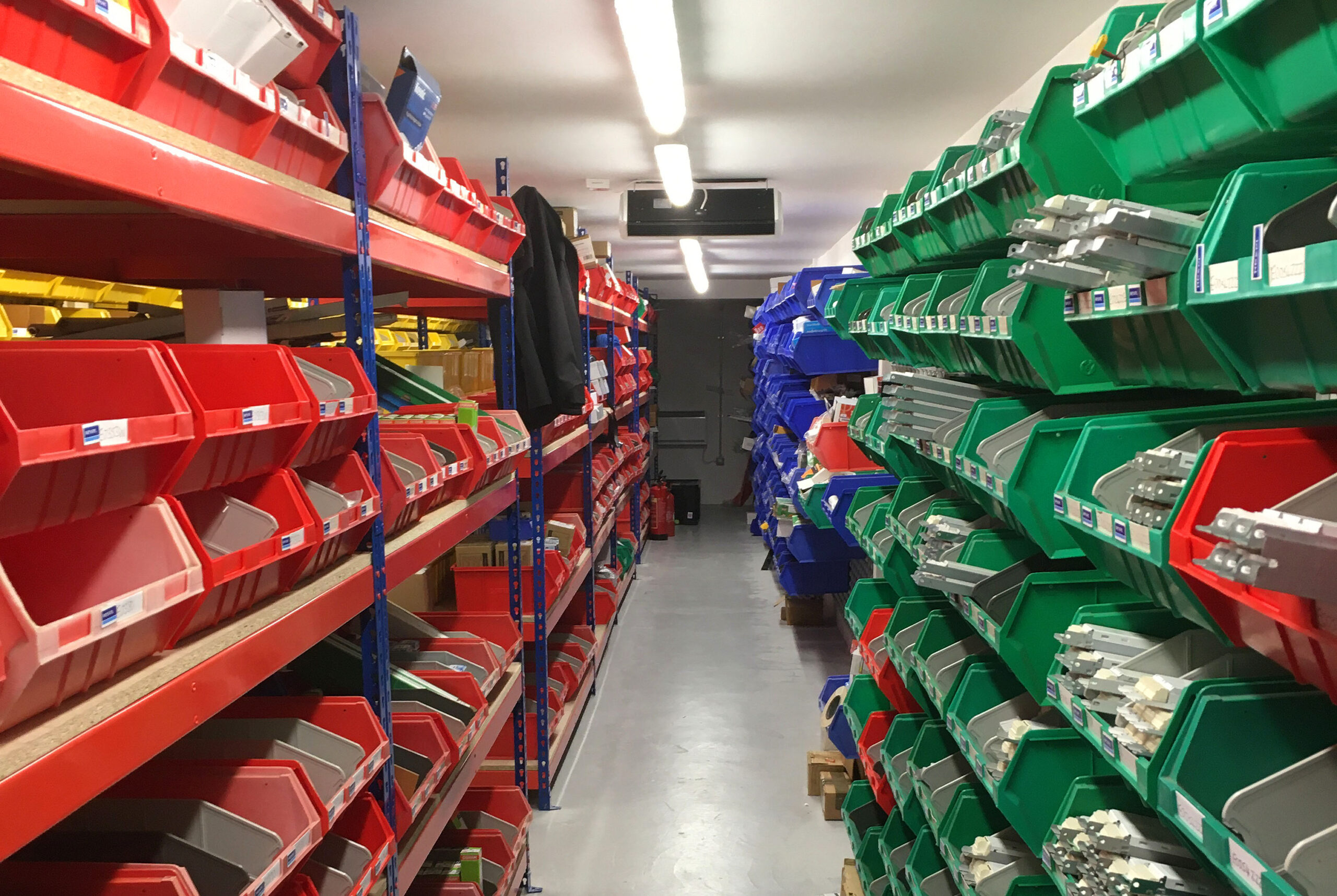
The challenges of inventory management are vast and complex. Many businesses have limited visibility of materials used in their operation, with inventory often stored in multiple untracked locations where usage is inadequately controlled, and replenishments are performed in a reactive way. The integration of innovative hardware combined with app-based inventory management technology is revolutionizing the way businesses handle their inventory. This offering numerous benefits that enhance visibility and efficiency.
Keeping track of stock levels can be a challenge, particularly when stock is held at separate locations, for example in various areas of a large store, or divided between several regional stores. With app-based systems, businesses can track inventory levels in real-time, ensuring that stores’ inventory levels are always accurate and up to date. This eliminates the risk of overstocking, while optimising inventory turnover.
In many businesses, particularly service providers, stock is often also stored across a fleet of vans. This can make it difficult to monitor stock levels, which in turn makes it problematic to spot where excess stock has been ordered or where stock levels are running low. Too many businesses are relying on manual processes that inevitably increase inventory errors and inaccuracies. In a recent article, Finance Online confirmed ‘It’s alarming that many businesses, particularly SMBs, are still not utilizing inventory management systems for operations. Moreover, some don’t even have a way to track their inventory.’1
Inadequate inventory management results in delays and time wasted on jobs that cannot be completed efficiently due to unaccounted for stock-outs. Stock-outs can result in high emergency delivery or collection costs, just to enable a job to be completed, as well as an increased risk of costly production downtime. Other inadequacies with inventory management result in delays, inaccurate invoicing, and poor cash flow, which leads to excessive spend or overconsumption of some materials. According to IHL Group, ‘the estimated value of global inventory distortion among mass merchants and grocery retailers in 2020 is $176.7 billion for overstock and $568.7 billion for out-of-stock.’2
App-based Inventory Management systems
Spreadsheets, paper, and stand-alone systems can’t deliver the inventory accuracy and supply-chain visibility it takes to stay competitive in the digital world. In addition, traditional inventory management methods are often time consuming and prone to errors. Innovative hardware partnered with app based solutions are the future of inventory management.
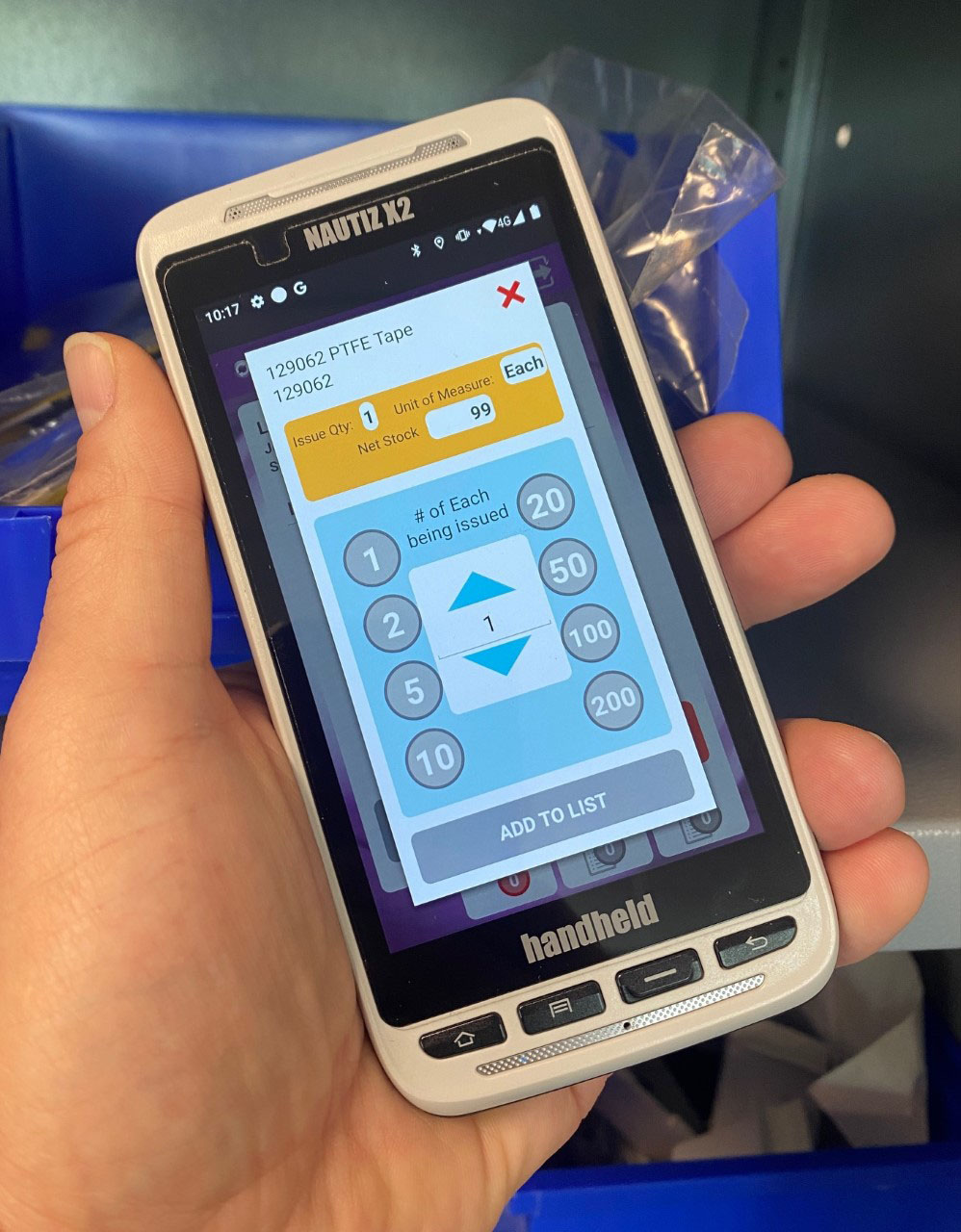
App-based store and van stock management systems are becoming more popular as supply-chain logistics become more complicated, and customers become increasingly demanding. According to Easy Post, ‘Companies can reap a 25% increase in productivity, a 20% gain in space usage, and a 30% improvement in stock use efficiency if they use integrated order processing for their inventory system.’3 Advanced mobile applications allow companies to manage their inventory and supply chains effectively. These systems efficiently record every scan and every movement of inventory and are designed to prioritise inventory accuracy, cost reduction, and charge capture through job number management. Businesses spend a significant amount of money on financing and stocking their inventory and it’s important to optimise this inventory to remain competitive. With extended lead times due to the pandemic, companies are having to invest more capital in inventory to ensure supply to customers.
In a McKinsey survey of global supply-chain leaders, it was found that 61% of respondents were either planning to increase or had already increased, the inventory of business-critical products in order to boost ‘supply chain resilience’ as a result of the pandemic.’4 And research from IHL found that inventory distortion costs in 2020, in the retail sector alone, cost retailers ‘collectively nearly $1.8 Trillion globally.’5 There are also ever-increasing expectations for improving Key Performance Indicators (KPIs) for customer service. Therefore, achieving inventory excellence, by optimising through app-based inventory management systems, is becoming increasingly important to support the customer-service function, improve cash flow and increase profitability.
Store and van stock management is being revolutionised with the use of inventory and supply-chain management apps on mobile devices. However, not all app-based inventory management systems are the same.
It is essential that the inventory management solution a business chooses has the functionality required to enhance the operations of the business
Leading-edge app-based Inventory Management systems:
- make use of the best technologies to manage the process
- can be used on specialised, rugged Android devices, such as Zebra and HandHeld, which utilise both laser barcode and Near Field Communication (NFC) capability
- utilise technology that speeds up the process of managing inventory
- are easy to use for operatives – the more intuitive the app, the easier it is for widespread adoption of the technology within a business.
The store is at the centre of all operational activity, responsible for stocking and distributing supplies such as tools, equipment, personal protective equipment (PPE), and supplies to employees, enabling them to fulfil their business requirements.
It is therefore essential that the inventory management solution a business chooses has the functionality required to enhance the operations of the business.
Critical Issues in the Automated Replenishment Process
Management of unit of measure (UOM)
The management of Unit of Measure (UOM) is particularly critical in the automated replenishment process, especially for a store where items are. usually issued in their smallest denominator (each individual item, pack, length, metre, etc.). However, the distributor or supplier will want the items reordered in bulk, e.g., a box of 200. It’s important that the software chosen can handle these conversions, ensuring there are no UOM errors in the replenishment process.
The integration with distributors is important in reducing inventory carrying costs and improving customer service.
Options for ‘unstaffed’ storerooms
When selecting an inventory software solution, businesses should think carefully about both the current state of their storeroom operations and what their ideal future state would be. For example, SmartStores, by Inventor-e, is often used in a staffed store during the day, but can also be used in unstaffed stores, with night-shift engineers issuing their job requirements while still maintaining stock accuracy. Some of our customers have also moved to completely unstaffed stores with SmartStores.
Offline capability
Despite best intentions, technology can sometimes run into issues and ways to minimise the impact on operations needs to be found. Offline capabilities are a critical feature of any store and van stock solution that allows you to store inventory data locally during a disruption in connectivity.
Integration with distributor systems
It’s important that distributors are onboard and convinced by the effectiveness of the technology for their customers, and also that the automated replenishment is seamless into their enterprise resource planning (ERP) systems. This ensures the whole supply chain supports the technology and the new process. This is one of the reasons that Inventor-e has a distributor policy: Wolseley being our exclusive UK distributor in the plumbing sector for Facilities Management (FM), and Rexel our UK exclusive distributor in the electrical wholesale sector for FM. The integration with distributors is important in reducing inventory carrying costs and improving customer service.
Advantages delivered by leading-edge Apps
Automated material replenishment
Optimised inventory levels can be maintained through automated restock triggers communicated directly to distributors and suppliers. The manual process of cycle-counting stock levels each time inventory needs replenishing is successfully eliminated by leading-edge apps.
Each inventory transaction is recorded, with demand signals generated automatically to the appropriate supplier, based on the desired replenishment method for each individual stocking location. This in turn eliminates stock-outs and shortages of materials assists businesses in avoiding making excess purchases, and consolidates purchase orders through nominated suppliers.
Distributors of SmartStores and SmartVan confirm that their customers’ operatives are completing, on average, an additional two jobs per day as a direct result of implementation.
Improved customer service through improved completion rates
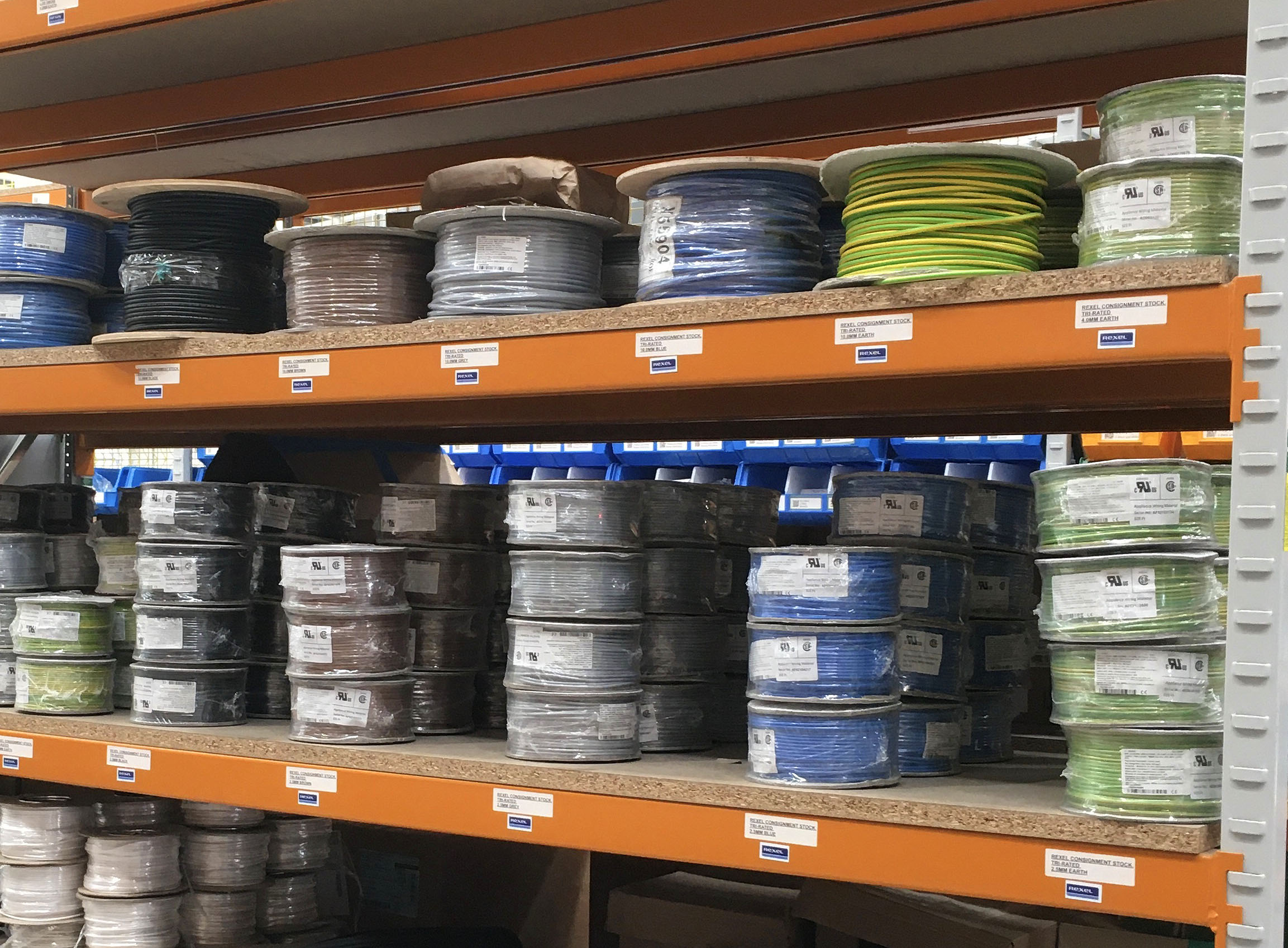
Leading-edge app-based inventory management systems offer businesses advantages with efficiencies in customer service by offering an automated solution to track, record, and reorder all materials and tools necessary to complete a job the first time.
Distributors of SmartStores and SmartVan confirm that their customers’ operatives are completing, on average, an additional two jobs per day as a direct result of implementation.
Real-time inventory capability across multiple stores and fleets enables:
- smarter scheduling decisions
- the avoidance of costly downtime spent chasing materials
- the ability to eliminate maverick purchasing and unnecessary trips to merchants and distributors
- more jobs to be completed per day by operatives
Rexel and Queen Alexandra Hospital, Portsmouth
Queen Alexandra Hospital, Portsmouth, is the largest Ministry of Defence (MOD) unit in the UK.
Inventor-e distribution partner Rexel worked with the hospital to overhaul their entire inventory management process using the SmartStores app-based inventory management system, which has resulted in the hospital achieving compliance levels in excess of 98% against their KPIs.
The problem
Before Queen Alexandra Hospital implemented SmartStores they were taking an irregular, paper-based approach to inventory management. Stock stores were staffed during the day, but not during evenings or weekends, and were accessed by multiple engineers leading to poor stock management and stock being used but not accounted for when re-ordering. Stock-outs were a regular occurrence, with engineers failing to complete jobs on time due to the parts they needed being unavailable. This resulted in wasted time through them going off-site to buy what they needed and being assigned to jobs that they couldn’t complete.
The company was being fined heavily by the NHS for failing to meet requirements, and it needed a reliable solution that would support the needs of the hospital while saving on time and cost.
The immediate impact
With SmartStores in place, Queen Alexandra Hospital now has a system that identifies the 5,000+ products it stores. Engineers have the ability to find the part they need, scan the items quickly, assign them to a job number and feel assured that the inventory will be reordered automatically for future use.
The wider impact
The Queen Alexandra Hospital now has a reliable app-based inventory management system with a live feed of which items are in stock and a full audit trail of transactions. Stock-outs have reduced drastically since the implementation of SmartStores, resulting in significant improvements in both staff and time efficiency as well as reducing unnecessary costs. With the rapid reduction in stock-outs, we have also substantially reduced the fines we were having to pay as well.
Wolsley and Livv Housing
Livv Housing Group is an independent housing association,
providing affordable, quality homes for around 25,000 people, through nearly 14,000 properties in Knowsley, Merseyside.
Inventor-e distribution partner Wolseley’8 worked with Livv Housing to install the SmartVan app-based inventory management system across the full fleet of 98 vans.
The problem
Livv Housing Group previously had no system to efficiently and accurately track stock held in their van fleet. Engineers had no
knowledge of inventory levels, or the cost of inventory on their vehicle, and had no way of knowing if they had the right products, they needed for the job they had been assigned. Engineers were wasting time being sent to jobs they didn’t have the correct parts for and were taking
multiple visits to trade counters to purchase items not stocked in their vans, resulting in lost time and overspend. There was also the problem of them not being able to complete a job first time because of the lack of correct stock in their van.
The immediate impact
With SmartVan in place, engineers are not only able to have an immediate view of the stock held in their own van, which enables them to successfully complete a job, but the central operational team at Livv Housing now has a real-time inventory of the stock held in each van, meaning that the right engineer can be sent to the right job with the right parts.
The wider impact
Livv Housing Group now has an efficient, automated system for
managing the inventory held in their van fleet. The number of repairs being completed per day has increased, due to engineers having the
right parts to complete the job in their vehicles, and their first-time fix rate has also increased. The time and financial costs of visiting the trade counter has significantly reduced, as has time spent on ineffective, manual inventory management processes.
Better yet, Livv Housing report a culture change within the business,
with engineers taking a greater sense of ownership and responsibility for managing the stock in their own vehicles, as well as reporting a positive environmental impact and saving on fuel, due to the reduction
Sustainability
There is an increasing drive within businesses to improve sustainability. An Oxford Economics survey, which interviewed executives from 73% of Consumer Product companies, stated that ‘sustainability issues were a major concern or top-of-mind at all stages of the supply chain process from planning, design, and R&D, through manufacturing, logistics/delivery, and product maintenance.’6 The implementation of app-based inventory management systems, particularly across van fleets, improves sustainability in a number of areas:
- optimisation of the replenishment process: unnecessary trips to merchants are eliminated as items are automatically reordered on the local branch when required
- operatives can check the stock of other vans and central stores to check inventory availability, saving wasted journeys
- stock visibility across the fleet of vans enables smarter scheduling of jobs and ensures operatives only visit properties with the correct materials for job completion
- ensuring assets such as power tools are not left behind on a job with the use of an app-and-assets tag prevents operatives from turning up to the next job without the tools to complete it, as well as preventing wasted journeys searching for lost assets.
In order for a business to be sustainable, it is. essential to know where every item is in real-time. When businesses do not have this information, they will experience overstock and out-of-stock situations, which result in excessive use of transportation and associated resource waste, less efficient use of storage space, and reduced customer-service levels.
The recent introduction of the SmartVan app into a managed inventory service across a fleet of vans significantly lowered unnecessary and unproductive journeys, saving time, money on fuel and also lowered the business’s carbon footprint.
App-Based Inventory Management Technology plays a vital role in the improvement of business efficiency and productivity, and customer service delivery, which in turn leads to reduced customer churn, reduced wastage, and increased profit. Stuart Axtmann, SmartStock Solutions Manager at Rexel, points out that the role technology plays is not to replace the jobs of store managers or purchasing managers, these roles are needed, it’s about giving the people responsible for these roles their time back to focus on ‘business critical activity, not the drudgery that the tech can remove.’7
How Inventor-e can help with our mobile optimised App solutions: SmartStores and SmartVan
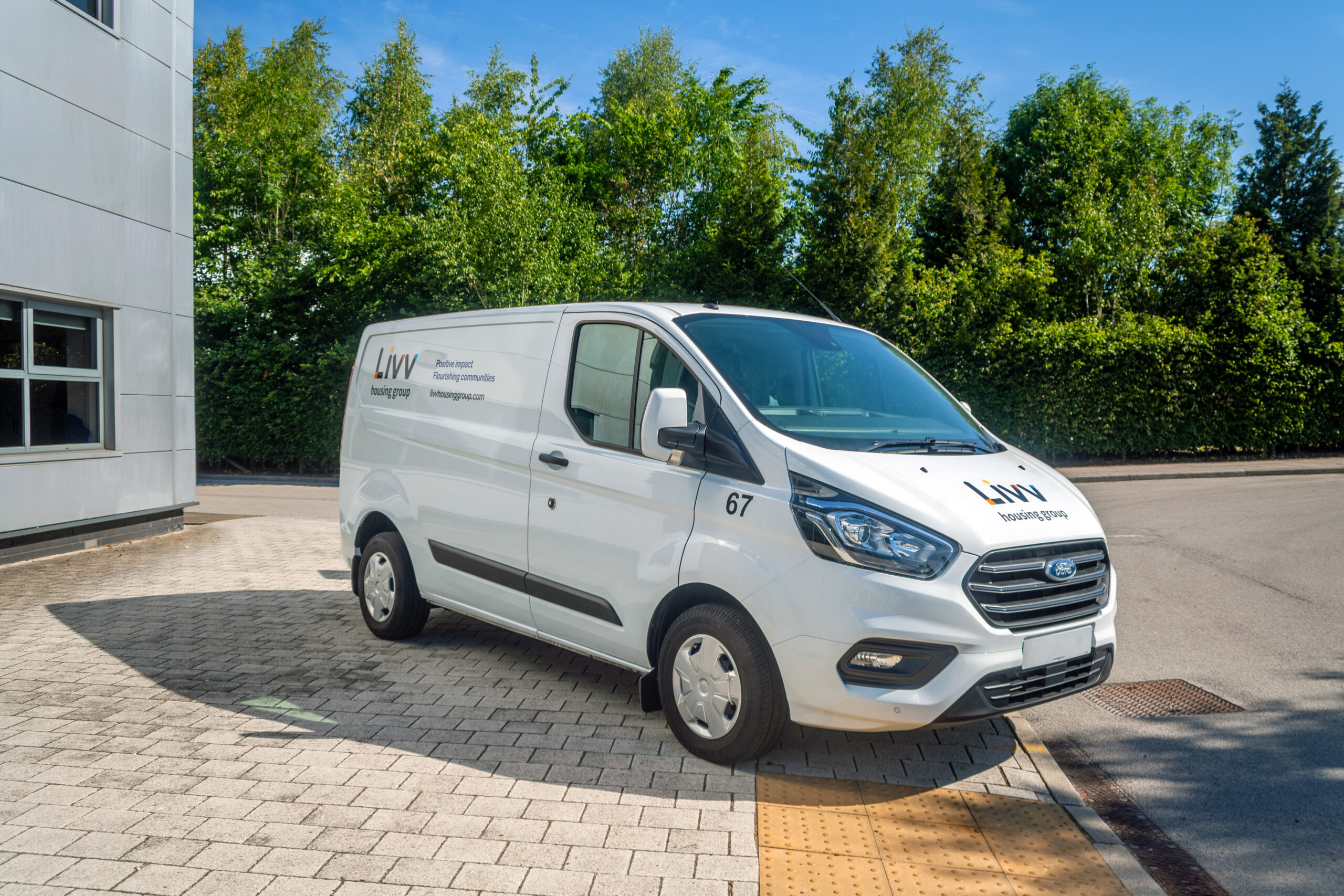
Easy-to-use mobile application
The SmartStores and SmartVan Inventory apps enable the management of inventory via a smartphone. This eliminates paper-based processes and enables businesses to instantly update inventory, in real-time, as transactions are performed.
A full suite of transactional capabilities captures material usage against job numbers, even without a cellular service, including the functionality for laser barcode scanning on specialist, rugged Android devices and contactless NFC.
Reorder levels, and minimum stock levels, allow monitoring of inventory to predetermined states, which means that products don’t have to be ordered every time the app is used. For example, if a van holds ten batteries it can be restocked when it’s down to its last four, while the main warehouse holds 1,000 batteries and is restocked when the level falls below 400.
SmartStores can translate clock cards straight into the app at the trade counter (see SmartStores video at www.inventor-e.co.uk), allowing all issuance and return transactions from a store to be seamlessly recorded against each operative. This adds a level of control and accountability across business and is particularly useful when managing many people across multiple stores.
Mobile/cloud technology
The SmartStores and SmartVan app-based inventory management systems are mobile/cloud-based technology, meaning that no supporting software is required to successfully use the apps. The architecture and quality of the cloud-based platform that aggregates the data from the van and stores management apps provide real-time visibility and control of inventory.
Real-time visibility and control through leading-edge cloud-based software, Sourcerer
The Inventor-e cloud-based software, Sourcerer, is a leading-edge platform that is fully scalable and has the capability to manage multiple suppliers in the supply chain into numerous stores regardless of geography. It can also manage the inventory and assets across van fleets. As inventory is depleted in a store, or van, it is automatically ordered from the appropriate supplier or can be set up to order from a central store, with the store generating the requirements for the supplier as inventory is depleted.
SmartStores and SmartVan reduce carrying costs, avoid excess purchases and increase the number of jobs that can be completed per day.
Real-time inventory visibility means operatives can see exactly what inventory is on hand across an entire business, including all warehouses, storage areas and vans. The SmartSearch facility allows operatives to scan an item’s barcode or NFC tag, or select an item from a search to display stock quantities across all stores and vans (by registration number).
Robust and easy-to-use reporting
Reports deliver all inventory data to help managers identify trends, opportunities, and issues that need to be addressed. Many inventory management systems have reporting capability, and when deciding on the right solution for your business it’s recommended that example reports from the system are reviewed to ensure the format, report type and available customisations will fulfil the business’s requirements.
With modern mobile technology linked to the cloud, businesses have the ability to create, manage and view customised reports against KPIs.
Return on Investment (ROI) through improved efficiencies
SmartStores and SmartVan reduce carrying costs, avoid excess purchases and increase the number of jobs that can be completed per day through:
- tighter controls for issuance and tracking of all inventory transactions to provide a clear audit trail down to the employee, job, or customer
- real-time visibility of the inventory in every van, and in every warehouse or stockroom, that enables items to be found quickly and easily by browsing, searching, or scanning the barcode or NFC tag
- charges that are captured against specific job numbers to ensure the inventory consumed is applied to the correct job: any items returned to the van and job are automatically deducted from the job’s cost
- integration to distributors, which offers seamless replenishment of inventory.
Enhance Inventory Management with complimentary solutions
SmartStores and SmartVan apps work with other Inventor-e solutions that further enhance control and security of inventory. These include:
- Smartie asset tags,
- iBinScale (a battery-powered weight sensor bin), and
- SmartStores Secure, a metal lockable cabinet accessed by the SmartStores app.
Further information
Contact us
e: info@inventor-e.co.uk
t: 0800 779 7214
w: inventor-e.co.uk
Sources
1. ’97 Supply Chain Statistics You Must Know: 2021/2022 Market Share Analysis & Data’, viewed 21 March 2022, https://financesonline.com/supply-chain-statistics
2. ’Disrupted Retail – How the Pandemic Exposed Retail’s Hidden Inventory Distortion’, viewed 21 March 2022, https://www.ihlservices.com/product/disrupted-retail/
3. EasyPost, 2019, ‘Top Reasons to Automate Your Fulfillment Operations with EasyPost’, viewed 21 March 2022, https://www.easypost.com/blog/2019-02-25-top-reasons-to-automate-your-fulfillment-operations-with-easypost
4. McKinsey, 23 November 2021, ‘How Covid is Reshaping Supply Chains’, viewed 21 March 2022, https://www.mckinsey.com/business-functions/operations/ our-insights/how-covid-19-is-reshaping-supply-chains
5. ’Anyone See Canada? Retail’s $1.8t Inventory Distortion Issue’, viewed 21 March 2022,
https://www.ihlservices.com/product/inventorydistortion
6. ’The Sustainable Supply Chain Paradox’, viewed 21 March 2022, https://www.sap.com/cmp/dg/sustainable-cp/index.html
Interviews
7. Axtmann, S, SmartStock Solutions Manager, Rexel, interviewed by Inventor-e on 28 February 2022.
8. Harnick, A, Regional Sales Manager – Managed Services, Wolseley, interviewed by Inventor-e on 28 February 2022.