The importance of Just-In-Time inventory management systems has gained prominence in manufacturing and supply chain strategy. This blog explores both the pro’s and con’s of JIT and gives you actionable advice on how to implement it effectively.
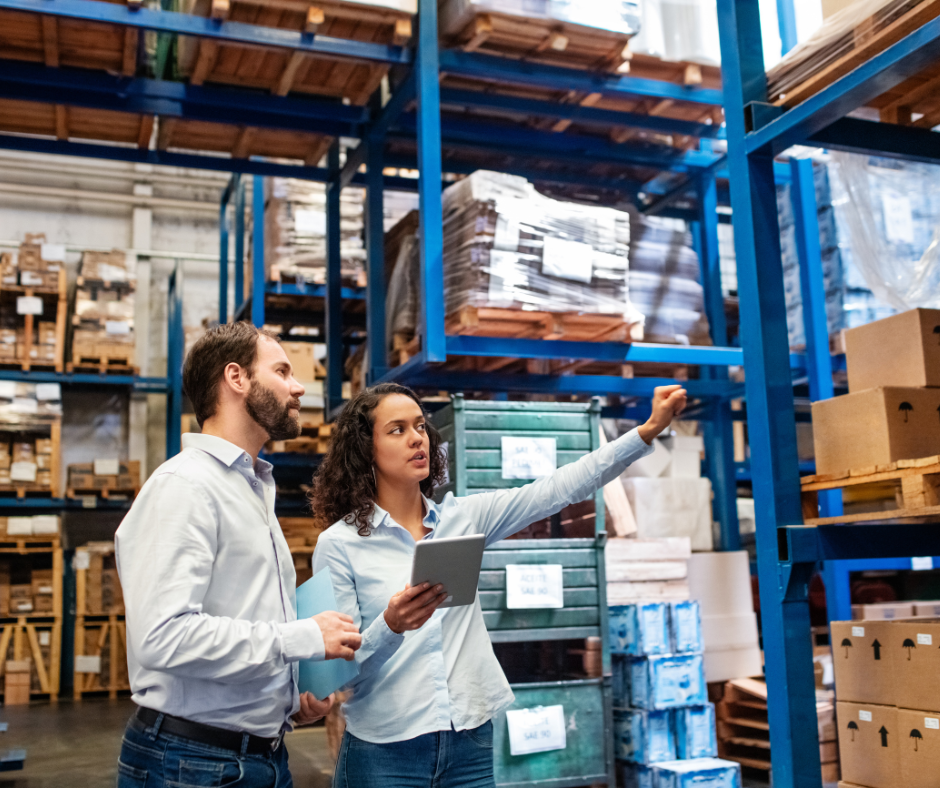
What are Just-in-Time inventory systems?
JIT inventory systems refer to management strategies that correspond inventory orders from suppliers directly with production schedules. Also known as the Toyota Production System (TPS), JIT systems aim to always have the exact amount and type of inventory needed, so as little inventory as possible is kept on hand. JIT inventory management is a strategy that has revolutionized supply chain operations across various industries. At Inventor-e, we understand the nuances of JIT and are here to help you leverage its benefits for your business.
Why is JIT inventory important and how does it differ from JIC?
JIT systems could increase your business efficiency and improve profit margins if executed carefully. By producing goods only when they are needed, businesses can significantly reduce the costs associated with storage and overproduction. This strategy not only helps in minimizing waste but also enhances the overall efficiency of the production process. Like any strategy, JIT comes with advantages and disadvantages. Understanding these can help businesses make informed decisions about whether JIT is the right approach for them.
Contrary to the Just-in-Time system is the Just-in-Case (JIC) system; the JIC system is a stock control method that involves ordering stock with buffer stock in place. This means that there is always stock available when required, eliminating stockouts and allowing businesses to keep up with supply and demand. However, due to buffer stock being held, more warehouse space is taken up, increasing warehousing costs.
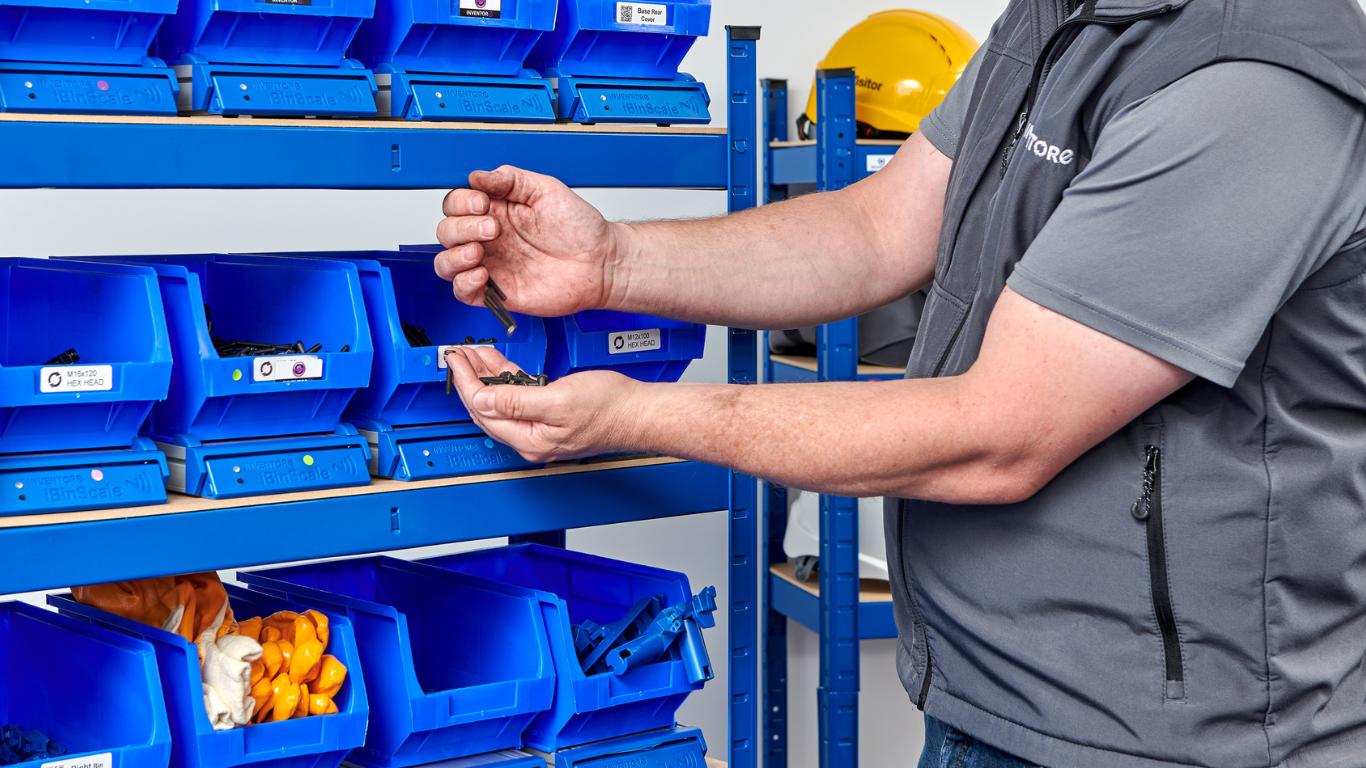
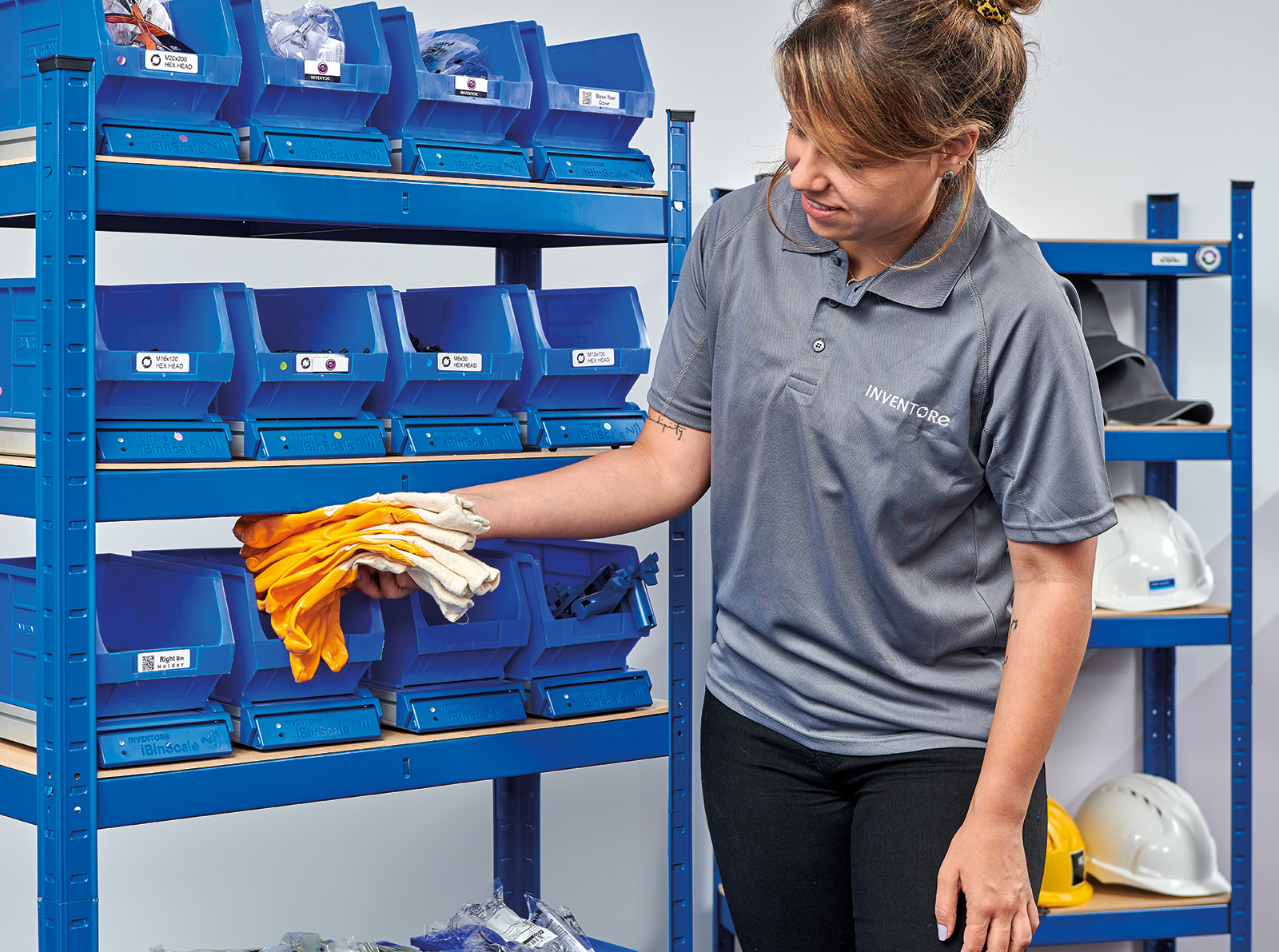
JIT Benefits
Like the JIC system, JIT systems have many advantages, some being:
- Reduced Waste
If a company works with fresh produce or items that have an expiration date, JIT systems reduce the disposal frequency of these items as, due to no excess stock being held, there is an increased chance of all items being sold before their expiration date is exceeded.
- Reduced Storage Costs
JIT systems receive inventory only as they need them, so no excess stock is held in warehouses. This reduces storage costs as less space is being occupied.
- Increased Efficiency
JIT systems promote a streamlined production process, reducing lead times and enhancing overall efficiency. This can lead to quicker response times to customer demands and changing market conditions.
- Improved Quality
As JIT systems focus on reducing defects in items and improving the production process, higher product quality is often subsequently achieved. This can result in fewer product recalls, warranty claims, and customer complaints.
- Lowered Loss Risk
Large product orders have no guarantee of being fully sold to customers, and so JIT systems mitigate this risk by ordering a smaller number of items at a time. As items are ordered only as and when they are needed, there is greater ability to abandon products that are no longer selling well, as your profits will take less of a hit than if you had bulk ordered to hold excess stock.
Cons of JIT Systems
- Leaves No Room for Error
If a shipping window is missed or an item is manufactured at a slower pace than usual, businesses will not have the right items at the right time.
- Supply Chain Vulnerability
Heavy reliance on suppliers makes the supply chain vulnerable to disruptions such as natural disasters, geopolitical events, or supplier bankruptcy. This can result in production delays and shortages.
- Information Dependency
Successful JIT systems rely heavily on accurate and prompt information regarding demand, supplier capabilities, and production processes. Inaccurate information can lead to stockouts or overproduction.
- Increases Risk of Stockouts
JIT systems run the risk that you won’t have enough stock of an item to meet demand. Stockouts can dramatically decrease customer satisfaction.
- Offers Less Pricing Flexibility
As you must replenish stock as soon as you sell it, JIT inventory systems don’t give you the luxury of waiting for the best price. If your supplier charges extra for your order due to extraneous circumstances, your profit margins will take a blow.
Implementation
A company famous for its implementation of a JIT system is the Toyota Motor Corporation. Kiichiro Toyoda, the founder of Toyota Motor Corporation, invented the Just-In-Time System in 1938, but it wasn’t fully realised until 1954.
The JIT system is something the company still uses today in conjunction with other systems Toyota has implemented. The system allows Toyota to minimise inventory of vehicle parts, boost work efficiency, and ensure components fit perfectly together first time as there are no alternative parts.
During the initial time when the JIT system was being implemented, the system nearly caused the company to come to a halt in February 1997, after a fire at one of their suppliers stopped their ability to produce a specific component needed for Toyota’s vehicles. Because this supplier, Aisin, was the sole producer of this component, its weeks-long shutdown caused Toyota to halt production.
This caused a ripple effect, where other Toyota parts suppliers had to temporarily shut down because the automaker had no need for their parts during that time. Consequently, this fire cost Toyota 160 billion yen (or approximately £420 million at the time) in revenue. As such, proper implementation and cautionary measures must be taken for a JIT system to run smoothly.
To ensure the smooth-running of a JIT system, you must meet the following criteria:
- Choose a reliable supplier.
- Have good communication with suppliers.
- Train employees on JIT principles.
- Deploy route planning software.
- Ensure you have a clear schedule for specific components/products and for the date you require them.
- Establish predictive processes. Develop demand-sensing and forecasting processes that are closely linked to inventory levels.
- Digitalise documentation processes. This can be done through cloud-based software platforms such as Sourcerer that interact with hardware, like IoT solutions that automatically reorder inventory when reorder point is reached such as iBin Scale, TwinBin Live and iClick.
By understanding the pros and cons of JIT, you can make informed decisions that drive your business forward. Let Inventor-e be your guide in this journey towards operational excellence and sustained growth. Contact us to explore how our digital inventory management solutions can empower your business and transform the way you manage inventory in the digital age.