In any industrial or manufacturing setting, the efficient management and control of materials within a storeroom environment are paramount. Ensuring that materials are readily available when needed, minimising waste, and optimising inventory levels are critical aspects that can significantly impact operational efficiency and the bottom line. Fortunately, with the advancement of technology and innovative solutions like SmartStores by Inventor-e, companies can streamline their material management processes to achieve greater control and cost-effectiveness.
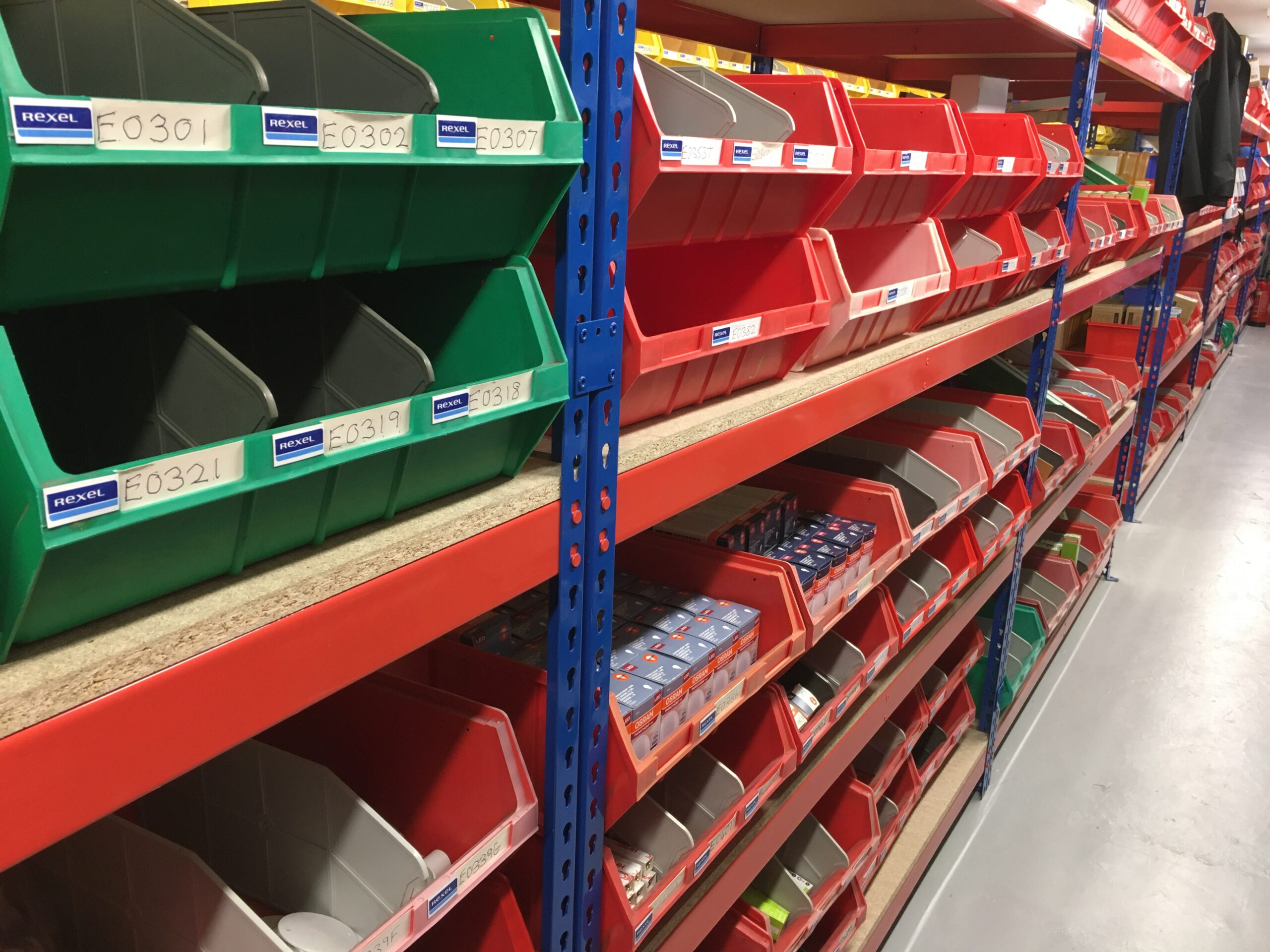
Understanding the Challenge
The management of materials in a storeroom environment poses several challenges. One of the primary challenges is maintaining accurate inventory levels while ensuring that materials are readily available for production or maintenance activities. Inefficient material management can lead to stockouts, excess inventory, and increased carrying costs. Moreover, without proper controls in place, there is a risk of theft, loss, or misuse of materials, further exacerbating the problem.
Implementing a Comprehensive Solution
To address these challenges effectively, companies can leverage advanced material management solutions offered by industry leaders like Inventor-e. These solutions utilise cutting-edge technology to provide real-time visibility into material usage, streamline procurement processes, and enforce strict control measures.
Key Features and Benefits
- Inventory Tracking and Visibility: SmartStores offers unparalleled inventory tracking and visibility, allowing businesses to monitor stock levels accurately in real-time. This visibility helps prevent stockouts and ensures that materials are replenished promptly to meet demand.
- Usage Control and Authorisation: SmartStores comes equipped with robust user authorisation and access controls, enabling companies to restrict access to materials only to authorised personnel. This helps prevent unauthorised usage or theft, enhancing security and accountability within the storeroom environment.
- Automated Replenishment: With automated replenishment mechanisms in place, companies can set up reorder points and triggers based on consumption patterns. This ensures that materials are restocked proactively, eliminating the risk of production delays due to stockouts.
- Usage Tracking and Reporting: SmartStores provides comprehensive usage tracking and reporting functionalities, allowing businesses to analyse consumption patterns and identify inefficiencies. With actionable insights, companies can make data-driven decisions to optimise inventory levels and procurement processes.
- Integration with ERP Systems: SmartStores seamlessly integrates with enterprise resource planning (ERP) systems, enabling companies to synchronise material management activities with other business processes seamlessly. This integration ensures data accuracy and consistency across the organisation, facilitating better decision-making and resource allocation.
Case Study: Realising Operational Efficiency
Conclusion
Efficient management and control of material usage in a storeroom environment are critical for maintaining operational efficiency and reducing costs. With SmartStores from Inventor-e, companies can gain real-time visibility into inventory levels, enforce strict control measures, and optimise procurement processes. By leveraging these capabilities, businesses can streamline their operations, minimise waste, and achieve sustainable growth in today’s competitive landscape.
Don’t let inefficiencies cost your business time and money. Partner with Inventor-e to achieve better material control today. Ready to take your material management to the next level and revolutionise your storeroom environment? Discover the power of SmartStores today!